
特集「仕立てへの拘り」#3 組立
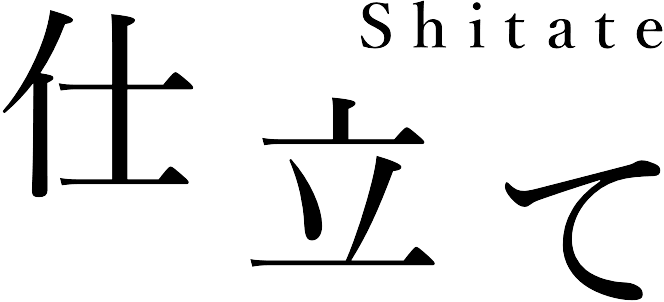
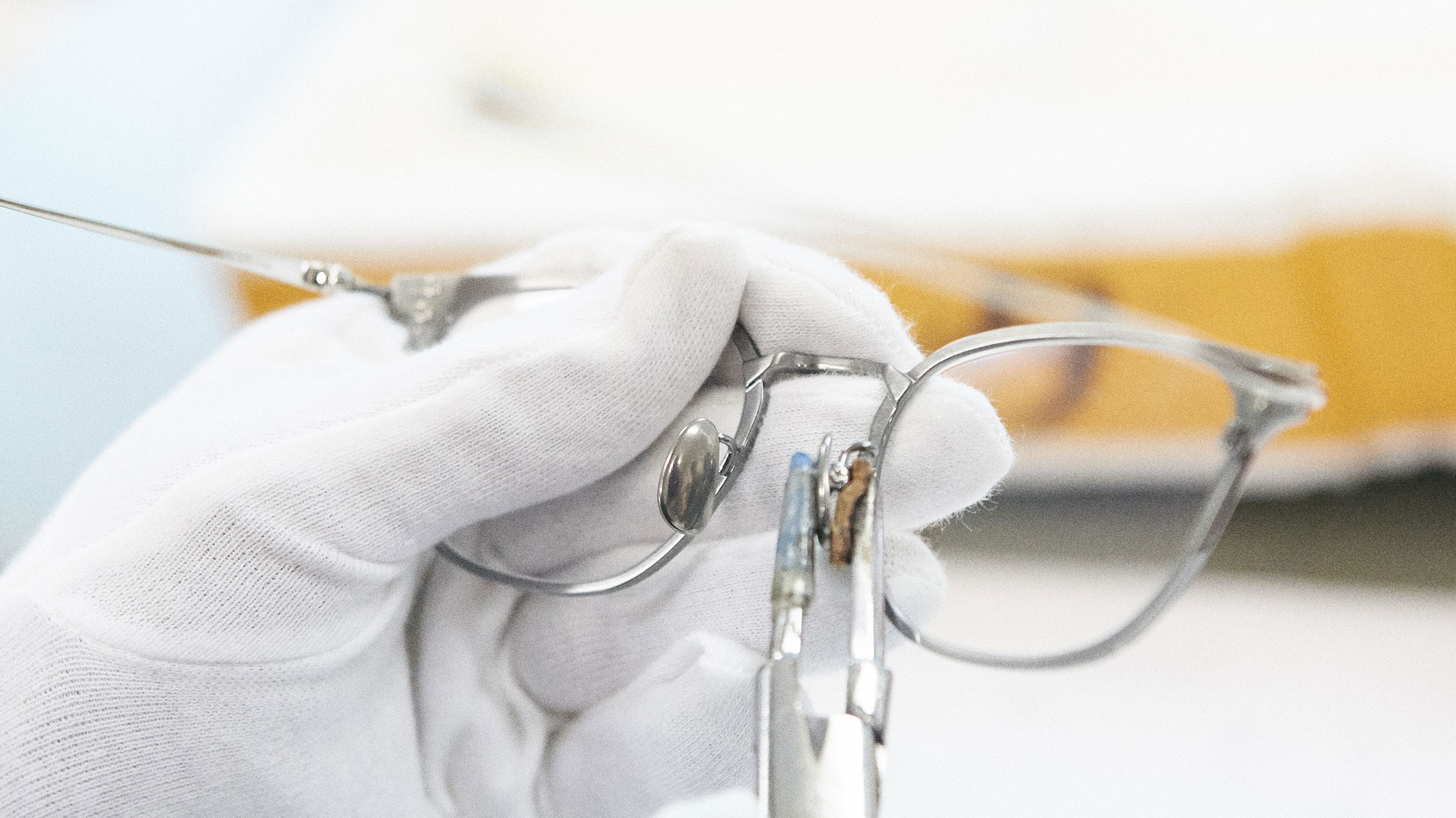
第三弾の今回は、ブランドの眼鏡造りを統括するミヤシタオプトメークさんにお話を聞いてきました。
その言葉からは、世界的な眼鏡産地鯖江の歴史と、モノ作りへのこだわりを感じることができます。
また、コロナ禍に巻き起こった鯖江の現状がよくわかる内容となっておりますのでご覧ください。
コロナ禍後の鯖江の現状と課題
対談
Toshihiro Miyashita
有限会社ミヤシタオプトメーク代表取締役社長
脇 まずプロフィールを簡単にお聞かせいただけますか?
宮下 会社の創業は約70年前、父が始めたこの会社を継いだ2代目です。最初、父は日産眼鏡という眼鏡会社で働いて、その後独立しました。
脇 当時の鯖江と今の鯖江を比べるとどうですか?
宮下 当時と今を比べると、たとえばうちで言えば、プレスでもなんでも自分たちでやっていたので、ここにももっとプレス機械が沢山置いてありました。
脇 ええ、そうなんですか。
宮下 はい、親父の時代は、例えば真鍮が材料であったりとか、素材も今と違っていたり。それほど難しい技術のものでもなかったと思うので、今から思えばもっと簡単な内容しかできないレベルだったのかもしれませんね。プラスチックを火鉢みたいなもので温めたりですとか、今ではもう見れない景色の中で、小さな頃から生まれ育ちました。
脇 社長になったのはいつ頃なんですか?
宮下 ちょうど、30年前ぐらい前ですね。大学を卒業した後、28歳で福井に帰ってきて、野尻眼鏡さんに3年間お世話になりました。その後この父の会社に入り、35歳のときに社長になっています。時代的には、サラリーマン時代がちょうどバブルのころだったので、そのバブルのあとぐらいです。↗
脇 それってアラレちゃん効果で黒縁眼鏡が流行った頃ですか? 確かあまりの人気に黒生地が不足し、生地素材がメーカーに届くと、荷下ろす前に奪い合いになっていたという都市伝説があります(笑)。
宮下 いや、ドクタースランプアラレちゃんのときは、自分はまだ高校ぐらいの頃だったと思います。まだあの頃は、仕事としてメガネには関わっていませんでした。
脇 眼鏡産業の1番のピークっていうと、あの80年代とか、そのあとぐらいになるんでしょうか?
宮下 そうですね、ピークっていえば2000年ぐらいですか、いやでもピークをどう考えるかにもよりますけど、もしかしたら、今がその1番のピークなのかもしれない(笑)
脇 あーそうですね、以前も仰っていましたけど、こんな状況は初めてだってお話しでしたもんね。
宮下 そうそう(笑)。コロナ禍になってからですから、今から2年ぐらい前になります。世間的には、まだまだ行動制限もあり、コロナの渦中と言える時期でしたけど、あの頃からずっと今にまで続いています。それまでは受注から3、4ヶ月後には商品を納品できていて、これまではそういう感じで何十年も続いていたし、暇な頃なら2ヶ月程度で収められることもありました。すでに金型が存在しているリピート品の発注であれば、ほんとに2、3ヶ月で仕上げるのも当たり前だったのが、いつのまにか納期が半年になり、そして10ヶ月になってしまう、という状況にまでおちいっています。
脇 商品を注文する自分としましても、以前なら半年ぐらいで計画を立て発注をしていましたけど、今は1年後の依頼をさせてもらっています。
宮下 脇さんとの出会いは、脇さんがまだ前の会社にいたときからですね。
脇 あの時は、もともとお願いしていた眼鏡工場が、忙しくてどうにもならない状況だったんです。こちらも展示会まで残り2ヶ月という切羽詰まった状況だったんですけれど、もうどうにもならないというところまでなってしまっていて。展示会までの日数がなくて、展示会用サンプルが間に合わないかもしれないというかなり厳しい状況でした(笑)。そこで宮下さんに急遽お願いさせてもらったのが、宮下さんとのお仕事を始めるきっかけでした。それまでは意外にもつながりがなかったんですよね。↗
宮下 でもあのときにはカルチャーショックがありました。マックスさんの作るパーツのレベルを体験して、これからはこういう作り方が必要だよなという衝撃を受けました。MAXさんはとにかく高い技術を持っているので、こちらの作業もスムーズで。
脇 たまたまマックスさんにお願いしていた部品ばかりだったのもあったんですけど、そのときから、宮下さんとも相性が良かったのを僕も覚えています。マックスさんもとても喜んでくれていました。
宮下 ほんとうにクオリティが他の工場のものとは違っていました。単純にパーツっていうよりも、品質や美観を深く考えたパーツの作り方の発想自体がそもそも違っていて。例えば、ロー付けをしなくてもいい作りですとか、ばらつきの少ないパーツの質ですとか、精度がとにかく高いので、様々な工程もスムーズですし、商品の品質も一段と高められます。ロー付けはどうしても手作業になってしまうためばらつきが出てしまうものですけど、マックスさんのパーツは一体で製造するので安心感があります。
脇さんとのお付き合いはあの時からなので、時間でいえばそんなに古いお付き合いっていうわけでもなくて、今から8、9年ぐらい前、ちょうどブランドを立ち上げるちょっと前ぐらいからではないですか?
脇 そうですね、僕が独立したのが2017年で、4月にオフィスを立ち上げ、5月にオリジナルブランドをスタートすることを決めました。ブランドのことは最初にMAXの中林社長に相談をしたんですが、当初は以前からお願いしていたメーカーさんのことを考えていたんですけど、中林さんからも宮下さんがいいのではないかって助言を頂いていまして。それで立ち上げ時に、少量しか発注できないですけど、それでもいいですかって聞いたら、いいよとご返事をいただいて。
宮下 僕は少量が好きなんです。その方が楽しいですから。でも今数が増えてきて辛いんですけど(笑)。うちは元々、大量に注文をして頂くブランドを相手にしていた工場だったんです。でもあるときそういうのが嫌になって、14、5年ぐらい前から小ロットの多品種をオーダーしてくれるブランドとのやり取りの方へと、徐々に業態を変えてきました。何千枚っていうロット数の商品を作ることはその頃からしないようにしました。
脇 確かに他のメーカーさんは、大量のオーダーをっていうのが多いのですけれど、宮下さんと知り合った時に、小ロットならどうだって聞いて、それだったらって受けていただきました。
宮下 でもその小ロットの方向に変えて以降、関わっているブランドが皆さん調子が良過ぎてどんどんと数が増えていき、今や大変になってしまっています。ここ最近の異常さは本当に特別な状態で、もうこれ以上できないレベルになってしまって、今は新しいブランドは皆さんお断りさせて頂いているんです。
脇 そんな中でも作っていただいているのが、本当にありがたくて。
宮下 当時を思えば、まさかここまでのスピードで増えていくとは思わなかったですよ。でもリピートが安定して回ることもありがたいことです。もはや海外では偽物が出回っているみたいですしね(笑)
脇 宮下さんに教えていただいたあれには驚きました(笑)。社長から、脇さんこんなのありますよって連絡が届いたので見たんですけど、キービジュアルでモデルさんの画像までパクっていましたし、まさかあそこまで再現をするとは驚きました。↗
宮下 いや、パクられるのも一流の証拠ですよ(笑)。他にも丸山くんとかカメマンネンのもありました(笑)。脇さんに知らせたら、早速ご自分で買っていて。
脇 思わず買ってしまいましたけど(笑)。実際みてみると、Sラインのバネとかもうガチガチで(笑)。
宮下 材料はチタンです?
脇 チタンはチタンっぽいんですけど(笑)。流石にそういうところの荒さを感じるクオリティでした。
脇 以前お聞きしたことですが、ベータは磨きが難しい、平らな部分を磨かないと変形してしまうというお話もあったじゃないですか?
宮下 ベータチタンの素材で、このテンプルの細さを作るのはかなり難しいんです。磨くためのガラ研磨機の中に普通に入れてしまうと、パーツのフォルムが変形してしまいます。ベータって素材としては硬いものじゃないですか、あれをそのまま普通にガラの中に入れるだけではうまくいかないんですよ。それに胡桃チップじゃないと綺麗に仕上がらなかったりもします。普通にするだけではベータに艶が出てこないですけど、とはいえガラの中に入れすぎると、パーツのエッジが落ち過ぎてしまいクオリティが下がってしまう。チタンといえば鯖江の眼鏡にとって一番重要な素材なんですけど、実は使いにくい材料でもあるんです。
脇 よく工場さんからも、うちのテンプルは、難しい、難しい、って言われることも多いんです。
宮下 どうしてもブレてしまう下のところの浮面とか、形状が逆反りになってしまうケースとか、その辺も含めて全てを綺麗に磨く技術が大変なんです。いつも頼む磨き屋さんでも無理っていわれましたし、他のプラスチック枠工場にコンビをお願いできないかって頼んだこともありましたけどそれも無理でした。
宮下 だから外注先からは全て断られてしまっていて、うちでやるしかないんです(笑)。
脇 磨き屋さんには嫌がられる内容ですものね(笑)。↗
宮下 見ただけでいえば作れるって考える工場も多いとは思うんですけど、作ってみるとやっぱり勘弁してくれってなると思います(笑)。
でもここまで拘っている内容もどのぐらい届いているんですか?
脇 できるだけ伝えたいと思っていて、定期的にタブロイドを発行しています。でもまだまだ説明不足で、取り扱っていただいている小売店さんにも、ご利用いただいているユーザーの方々にも、伝えきれていないことがまだまだたくさんあります。できるだけ、いろいろな拘りを伝えていきたいとは常に思っているんですけど。
脇 表面処理もブランド立ち上げ以来一貫して美装ジャパンさんに頼んでいますけど、あのクオリティーもとニュアンスのカラーリングは他ではできないじゃないですか?
宮下 そう、他の工場に持っていっても、あの表現はできないです。
脇 あれは本当にすごいなと思っていて。
宮下 あそこまでいい感じにはそう簡単にはならないですよ。
脇 比べると本当に違いますよね。
宮下 あの手間暇のかかり具合を考えると、ある意味異常なんですよ。でもどうしてもこだわりが強い反面、脇さんのデザインの場合では、メッキだけでも、ややこしいものによっては、表見処理だけで2、3ヶ月も時間がかかってしまうことがあって。
脇 でも、ここでしか造れないものなんで、納期も単価もかかってしまうけど、でもやっぱりそこへのこだわりは大切にしたいんです。そのこだわりがテイラーの特徴だと思ってやっていますし、当然単価も納期もかかるけど、それでも、このやり方で今もお願いしているのが現状です。
宮下 表面処理は、眼鏡造りの中でも最後の方の工程ですけど、そこで時間がかかってしまうと、うちとしても納品できずに売り上げがいつまでも立たないという現実もあります。部品代は支払うのですけど、そこから完成するまで、そこで寝かされるわけですから、もうこれは黒字倒産もやむなしな状況とも言えまして...。昔なら2、3ヶ月だったものが、1年になってしまっているのですから、仕事はあるけど、商品を納品できないので、お金は入ってこないっていう状況でして。だから、一刻でも早く商品を仕上げたいですし、ほんと明日にでもすぐ納めたいんですけど。あのクオリティですから、人気もあってもう混みすぎてて。ちゃんと振り分けしたいけど、それもできないぐらい、とにかく異常な状態が鯖江で続いていて、2年ぐらいのコロナが少し落ち着いてきたあたりぐらいから、もう毎月のように下請けの加工納期が伸びてしまっています。
脇 テイラーとしても、遅れれば当然在庫がなくなってしまうので、それを計算に入れて新しいモデルでは、数を増やしたり対策をしているつもりなんです。けれどもそれは他のブランドさんも同じような状態になっているわけで、みなが同じような行動をとってしまい、こうして気がつけば、鯖江自体に、そうした循環が生まれてしまっているのが、今の現状だということになりますよね。
宮下 ご購入できずに予約のままお待ちいただいているお客様には、本当に申し訳ない気持ちなのですが、自然渋滞のように遅延が生まれてしまっているのが現状です。他のブランドの新型は断っているケースも多いです。
脇 それは金型部品製造工場のMAXさんでも同じみたいで、なかなか予約が取れないらしいです。↗
宮下 やはり皆さん、発注数量を倍ぐらいにしています。最近ようやく緩和してきた感じもありますけど、でも元々、眼鏡製造って正月と夏は暇っていうのが普通だったんですけどね、今までは。でももうここのところは、とにかくずっとフルスロットルで作業をしている状況ですね。
脇 こういう状況になるには何か要因はあったのでしょうか?
宮下 そうですね、まず海外からまとめて注文が入ってきたのがありました。それでまずアメリカが一気に復活して。
脇 私の知ってるレンズメーカーも、コロナでアメリカの売り上げが一旦ゼロにまで落ち込んだらしいのですが、その後異常な復活が起こったようです。
宮下 それと働き方改革以降日本人の労働スタイルも変わったので、それが返って首を閉めることもある。今は休日には仕事をしない企業も増えたので、これは言いにくいことですけど、昔だったらある程度無理してなんとかしていたところも、土曜には作業をしているとこも少ないですし、平日でも5時過ぎには電話が繋がらなくなってしまう会社も多くなって、6時過ぎだともうほとんど繋がらない。だから、今の時代ならではの、そういう社会のあり方が、この状況を悪い方へと後押ししていることもあると思います。とはいえ、ほんとうに申し訳ない気持ちでいっぱいなのですが。
脇 これは眼鏡ライターさんから聞いたエピソードですが、取材に行った七宝屋さんの玄関においてあるパーツが詰まったパレットが、取材中にもさらに山のように積み上がっていく姿をみたそうです。
宮下 まずコロナが緩和したあたりにアメリカからの注文が来て、それがアジア圏にも飛び火した。そして、ものが手に入らない状況になり、そうなるとさらに皆が欲しがるから、だれもが商品を抱え込もうとする。そういうことが、コロナが分岐点となって生まれて、そして今でも続いている。それと中国のゼロコロナの影響もあったと思います。この前聞いた話ですけど、中国の方でも、同じように納期が延びていて、10ヶ月以上にもなっているようです。その皺寄せは、当然日本にも影響を与えることになる。ただ今の時代らしく、工場でも二極化しているのもあって、暇なとこは暇だっていう話も耳に入るんですけど、自分たちの状況を考えると、正直うそやろって思ってしまうのですが…。これはブランド側でも同じようでして、二極化が進んでいるという印象です。売れているところはほんとうに売れているようです。
脇 ミヤシタオプトメークさんで扱っているブランドに固まっているようにも思いますね(笑)。
宮下 小ロットのお客さんだけを僕は受けるようになったんでこんなはずではなかったんですけど(笑)。小ロットって、作業の点から見たら、本当はめんどくさいんですよ、脇さんのデザインを筆頭に。(笑)
脇 でもこれも、大量生産には向かないフレームを世の中が求めているっていうことなのかもしれませんよね。今の時代ってネットでみんな情報を見るじゃないですか、特にコロナ以降、オンラインを使うことがさらに進みましたし。
宮下 でも注文がないよりありがたいことなので、ほんとうに嬉しい悲鳴なのですが…。今月や来月の売り上げがない、というような不安がないのは、正直ありがたいことなんです。けれどもお待ちいただいているお客さんに、十分に商品をお渡しできない現状にも、ほんとうに辛い気持ちになっています。まだかな、まだかな、とお待ちいただいているお客さんがいるわけですから、どうにかしたいんですけれど、どうしようもできない状態になってしまっていまして。今まで眼鏡業界に携わってきて、ここまで遅れてしまうのは、初めての状態です。(場所を工場内に移動し、調子取りを行う高木さんのテーブルへ。)
宮下 こちらが納品前の調子取りをしているところです。調子取りについて簡単に説明しますと、パーツを組み立て眼鏡のかたちとなったあと、最後に行う調整の作業のことです。先ほどご説明したように、ベータチタンは磨きが難しい素材ですので、ガラ研磨をする際にも、様々な工夫を重ねています。ただその一方で、研磨するパーツ自体に、どうしても個体差が出てしまうんですね。磨きを優先して工程を進めていくのですが、ただそうしますと組みあげたときの仕上がりに個体差がでてしまいます。
当然パーツの研磨は、組み上げる前のバラバラな状態で行いますので、それを組み上げた時にばらつきが出てしまうものです。そこで、そのばらつきを整え、個体差のない商品として仕上げていく作業を調子取りと呼んでいます。特に鎧、テンプル、箱足のあたりは、繊細な注意をはらって調整をします。テンプルの形状や左右のバランスを個体差なく整えたりすることは、数値化しにくい作業ですので、どうしてもヒトの感覚で整える必要があります。
脇 モダンを機械で曲げるところもありますけど、やっぱり宮下さんのように手作業でしていただくのが、商品のクオリティには必要です。メガネと他のプロダクト製品の違いといってもいいと思うんです。。全くメガネの製造工程を知らない人にとっては、金属の製品などはベルトコンベアからパーツが流れてくるようなイメージもあるとは思うのですが、実際には大きく違っている。眼鏡をプロダクトと呼びますが、自分にとっては、どちらかというと手工芸に近いような感覚があります。
宮下 そのニュアンスをもっとわかっていただけると、こちらとしてもありがたいです。
脇 うちの眼鏡はむずかしい方なんですか?↗
高木 ほんと冗談抜きで難しいですよ(笑)。
宮下 こうしてテイラーさん専用の調子取り職人がいるぐらいです(笑)。
高木 脇さんには満足していただいていないかもですけど(笑)。
脇 いえ、こうして手作業でしていただいて、本当にありがたいかぎりです。パーツをデザインをする上でも、こうした作業が少しでも楽になるように、工夫を重ねているつもりなんですけど、調整できるけど、変形もしにくい、ちょうどいい硬さのパーツを考えるのは難しいんです。ちなみに今、うちの商品で調子取りしているものはありますか?
高木 ちょうど今しているのだと、TS07がありますよ(TS-07とは、オースの工場品番。)。それとこのテンプルがまっすぐな状態のものが、テイラーの1番最初のモデルTS-01(ソル)です。これが調子取りをする前の、ほんとにまっすぐな状態。
脇 これはなかなか見れないものですね。
高木 ちょっとやってみましょうか? このパットなんかも、こうやってなぶってない(何もしてない)状態のものを、そう、ここをこうやって、これをこうやって…。↗
脇 そんなに曲げれるんですか(笑)。
高木 そうそう、こうやって、ちょうどこういう感じで、そう(とテーブルに置いてある図面に合わせながら、あまりにも素早いテンポで調子取りをする高木さん)。
こういう状態が、こう、ん? ああ、こういうことですね、これがこう、図面の指示がこうあるので(早すぎて追いつけない状態)。
脇 ちなみに高木さんは何年ぐらい調子取りをしてるんですか?
高木 えっと、もう何年になるんだろう(笑)。
脇 まさしくこれこそゴットハンド。これはもう動画撮りたいです(笑)。しかし、こんなにアナログな作業なんですね(笑)。
高木 そう、ほんとうにアナログな作業なんです(笑)。
宮下 ガラ研磨後の部品には、一つ一つにバラツキがあるので、大変だけど、脇さん、このやり方しかないんですよ(笑)。
脇 まっすぐなものを曲げる時は一発勝負なんですか?
高木 そうですよ、金属にいったん癖ついてしまうと、どうしてもしわみとか癖ついてしまうから、だから一発勝負。
脇 え、めちゃくちゃ怖いじゃないですか…。でも、これってセンスが出ますよね…調子取りって。高木さんありがとうございます。神の手を堪能できました(笑)。
数々の有名アイウェアブランドのデザインを手掛けてきた脇聡が、2017年AWに発表しオリジナルアイウェアブランド。仕立て屋(tailor)という言葉を元に考案したブランド名TAYLOR WITH RESPECTには、制作に関わった全ての人へ敬意が込められている。
持ち主の体に合わせて丁寧に服を仕上げる仕立て屋のような、掛け心地がよくデザイン性の高いメガネ作りがテーマ。オールメイドインジャパンのフレーム